Wire Drawing Processes
The first step in manufacturing LAN cables is wire drawing. Wire drawing is a process in which the wire is drawn through a die so as to reduce its diameter and increase the length. As this happens, its volume remains the same. The dies are flooded with lubricant which also serves as a coolant, increasing the life of the dies and keeping the copper wire from overheating. The result of this process is 5000 ft of a coil of 10, 12, or 14 AWG copper wire.
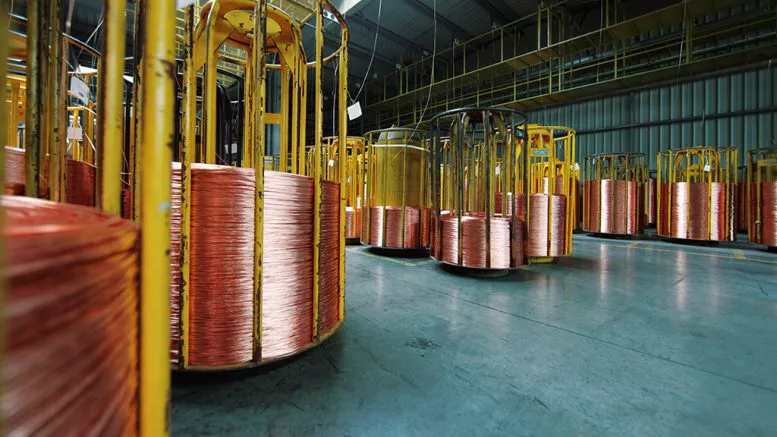
The copper wire produced in the first draw will then be transferred to an insulating area of the plant where a second wire draw will be done followed by annealing, before the application of insulation to the copper wire.
In the second wire draw, the size of the wire is reduced to 19, 22, 24, 26AWG, or to any size needed.
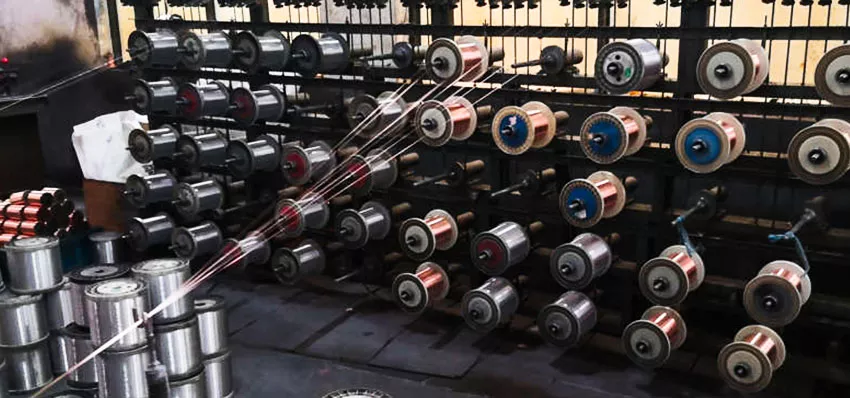
The drawing process work-hardens the conductor, leaving it susceptible to brittleness and cracking. Annealing equipment quickly raises the bare copper temperature to 450°F in a controlled nitrogen atmosphere to induce the appropriate metal softness needed to achieve desired elongation properties. Annealing makes the conductor workable and improves transmission performance, including, specifically, insertion loss.
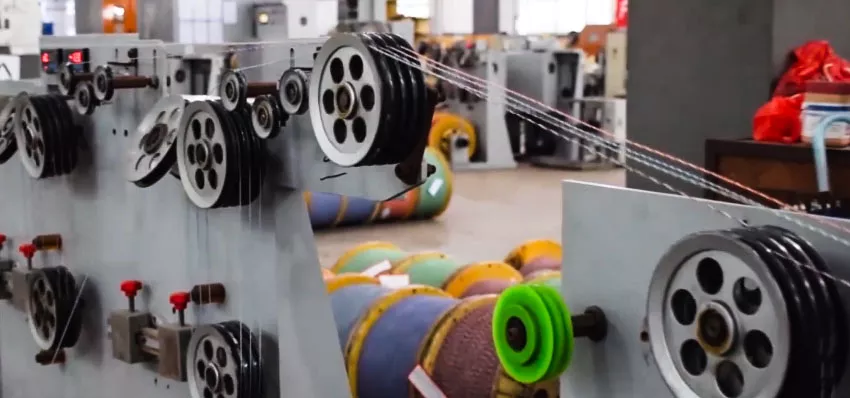
Applying Insulation
Wire Extrusion and Insulation
The next step requires the wire to be passed through an extruder where either a single or double coating of plastic is applied. High-density polyethylene pellets are fed into the extruder, heated and mets.
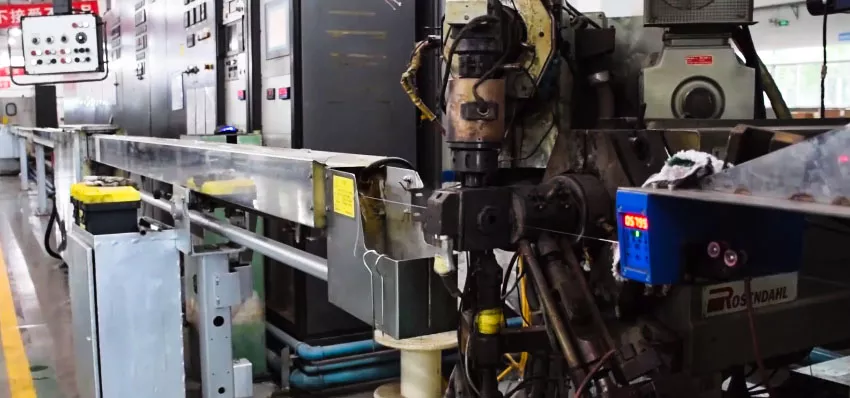
The insulation extrusion process consists of melting, homogenizing, and compressing (to release air bubbles) small, colorized thermoplastic pellets through an extruder head. The extruder feeds a crosshead, which is fitted with a wire guide (tip) and die. In this process, the insulation is applied over a preheated bare copper conductor.
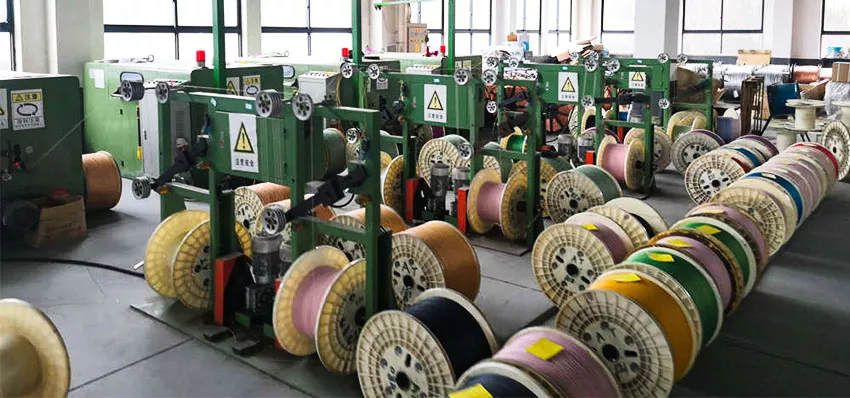
Wire Diameter and Insulation Testing
Before the reels move to the next manufacturing operation, wire and insulation diameter are measured, and the wire is tested for electrical properties as capacitance and resistance.
Twisted-pair design
Wire Twisting and Stranding
In this step, the insulated wires are twisted into wire pairs. Each pair has a unique twist length to avoid crosstalk and interference.
The wires will now be tested for electrical defects such as crosses, shorts, and opens.
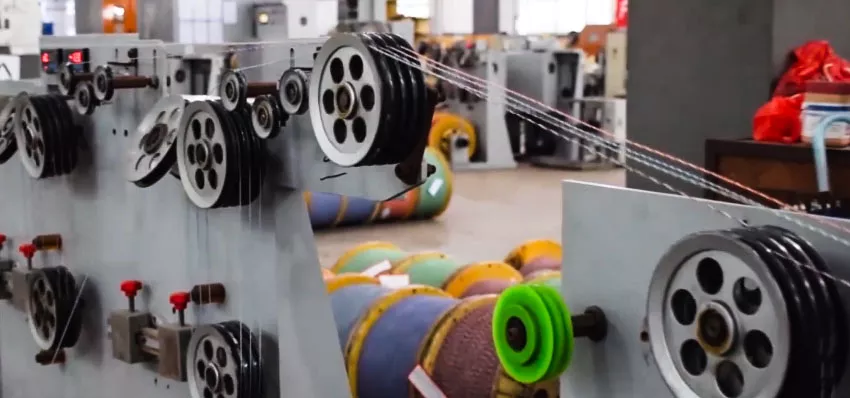
Manufacturing data-grade twisted pairs requires the use of pre-twisting equipment to prepare the conductor for the twining operation. Pre-twist machinery employs rotating bows that add torsion to each conductor prior to twining. This torsion induces the primary conductors to self-wrap during the twining process. This mechanical enhancement better controls conductor center-to-center distance within the twisted pair, allowing for improved return loss and impedance performance.

Because of the twisted-pair geometry, noise that is coupled onto the two conductors from an outside source (either an adjacent pair or from the cabling environment) appears equal in voltage magnitude and equal in phase. Equipment receivers, engineered to detect the signal difference between the two conductors, see induced noise as two “like” voltages, which are simply subtracted out during the signal reconstruction process. By design, each pair in a four-pair UTP cable has a unique pair-twist rate, or “lay,” to ensure crosstalk immunity from both outside sources and adjacent pairs.
Cabling
At this stage, the wires that came out from the stranding process are grouped together forming a multi-unit cable core. The units are also twisted together on a rotating core truck to help control electrical interference and provide flexibility.
Jacketing
At jacketing, several operations such as gel-filling, armoring, jacketing, and printing are performed to produce the finished cable.
Gel-filling and Armoring
The cable core is heated ensuring that the filling compound penetrates possible voids. A filling compound is added into the heated core in the filling chambers. Then finally, a plastic core is wrapped around the cable.
Metal Sheathing
Depending on the cable design, a protective metal sheathing of either aluminum or aluminum and steel combined may be added during this manufacturing step. The aluminum acts as a grounding path for high-voltage surges that may be caused by lightning strikes and other eventualities in aerial cables, while steel adds mechanical protection for buried cable against pests such as rats and gophers.
Extrusion of Outer Cable Jacket
The outer cable jacket is extruded in the next step. It is usually made from low-density polyethylene, black in color and resistant to ultraviolet light in case it is exposed to sunlight. This rugged plastic is the final protection for the enclosed cable against the environmental conditions underground or when strung to utility poles.
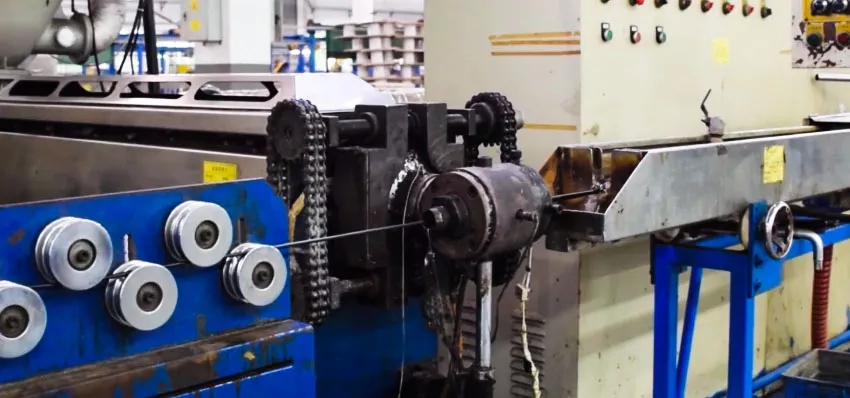
Cooling and Finishing Touches
The jacketed cable then passes through a temperature- controlled water trough, which cools the jacket. The cable is dried, and the top layer of the jacket is heated slightly so that printer markings can be imprinted on it. Because of the heating, the markings are stamped into the jacket itself and will last the life of the cable.
Jacketing a cable core primarily protects the finished product from handling damage and disturbance to the pair geometry. An optional ripcord may be incorporated over the cable core during the jacketing process.
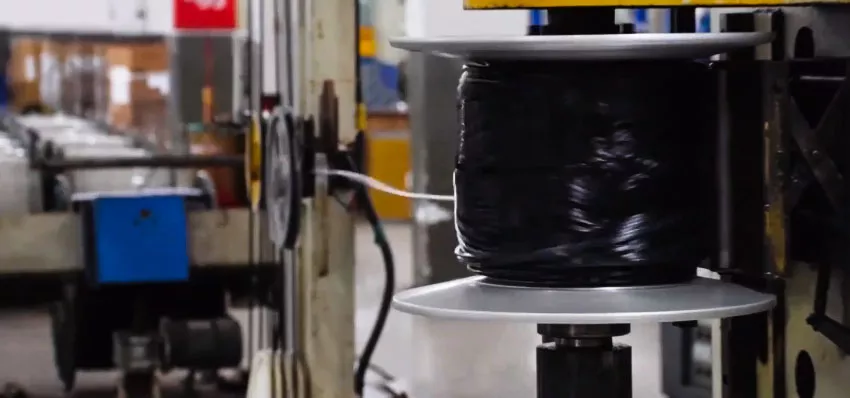
Cables Testing
Upon exiting the jacketing operation, the finished cable is wound onto metal or wooden reels and then transported to the final test facility.
Physical Inspection of the LAN Cable
An inspector checks for proper placement of units, subunits, and spare pairs within the cable.
Electrical Test
Electrical tests include a ring-out of all conductors for continuity, and a core-to-sheath test. The core-to-sheath test measures minimum voltage requirements between the cable core and the metal sheath; this helps ensure that high-voltage surges, such as lightning strikes, cannot reach the conductors. A high-voltage test is also performed, and all conductors are checked for electrical integrity. Random tests are performed for mutual capacitance, unbalance, and resistance.
Shipping
Preparing the cable for shipment may include sealing the cable end with a steel or plastic cap, and testing air-core cables for integrity. Such cables are equipped with valves so that dry, pressurized air can be pumped into them to protect them from moisture.